在碳達峰碳中和目標下,“零碳園區(qū)”“零碳工廠”已寫入2025年我國《政府工作報告》。作為黃河重大國家戰(zhàn)略明確支持建設的實體性新區(qū),濟南新舊動能轉換起步區(qū)正崛起一個智慧零碳工廠。4月19日,“黃河新動能·沿黃共未來”講好新時代黃河故事暨濟南新舊動能轉換起步區(qū)媒體采風行活動走進愛旭濟南工廠!绊椖咳孢_產后,預計年度節(jié)約用煤量2160萬噸,減少碳排放5384萬噸!睈坌駶瞎S項目管理總監(jiān)劉景喜說。
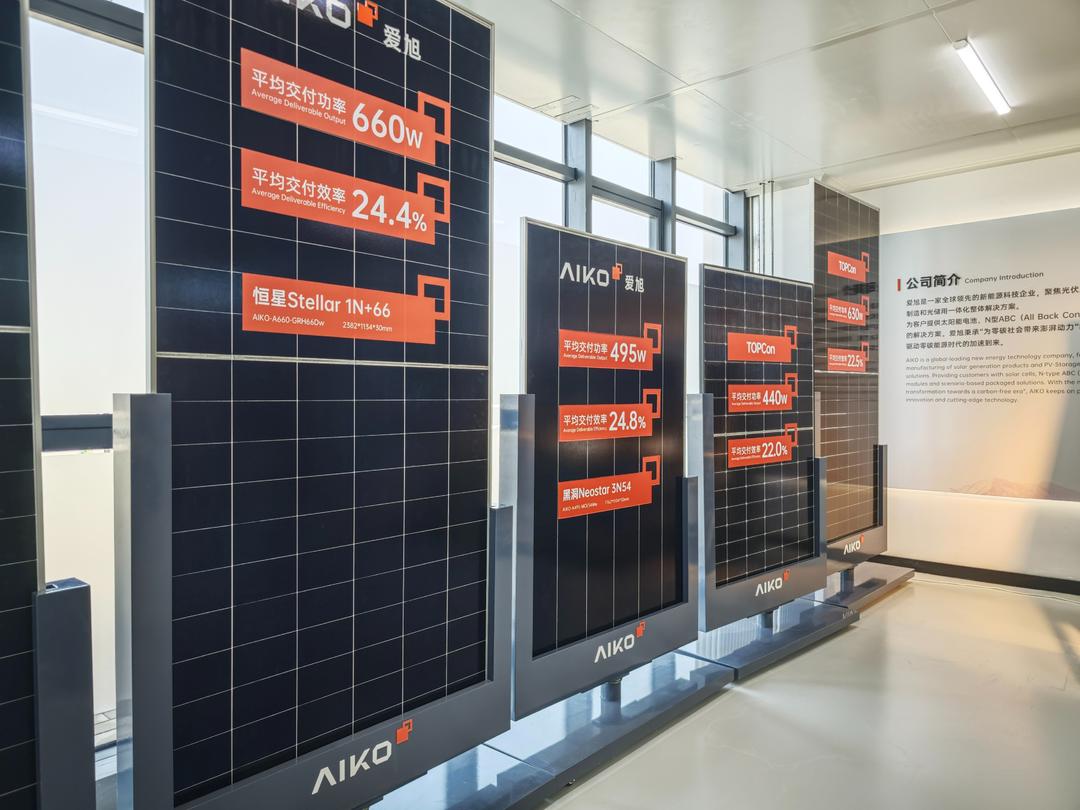
作為濟南引爆性項目之一,愛旭濟南工廠自落地以來就備受關注。該項目規(guī)劃總投入360億元,分三期建設,建成后可實現(xiàn)年產30GW高效太陽能電池組件生產能力。其中,一期項目組件車間2024年初開工,實現(xiàn)當年開工、當年建設、當年投產,創(chuàng)造了愛旭N型ABC電池組件先進產能最快投建紀錄。
走進愛旭濟南工廠組件車間,明亮潔凈,長長的走廊靜悄悄。穿過玻璃門踏進生產區(qū)時,方能聽到機器作業(yè)聲。長達330米的生產線,串聯(lián)起光伏組件的濕印、疊焊線掃、疊層等17個生產環(huán)節(jié)。
工業(yè)4.0的智能生產場景在這里生動呈現(xiàn),只見全自動的生產線一條龍有序運作,各種類型的機器人齊聚,揮舞手臂、靈活轉身、精準作業(yè),在不同的生產環(huán)節(jié)大展身手,工人大多只需要操作智能設備。
在終檢環(huán)節(jié),伴隨著“啪”“啪”的清脆聲,機器人將光伏組件上的插頭精準插上。擦拭殘膠這種作業(yè),也被機器人輕巧完成。
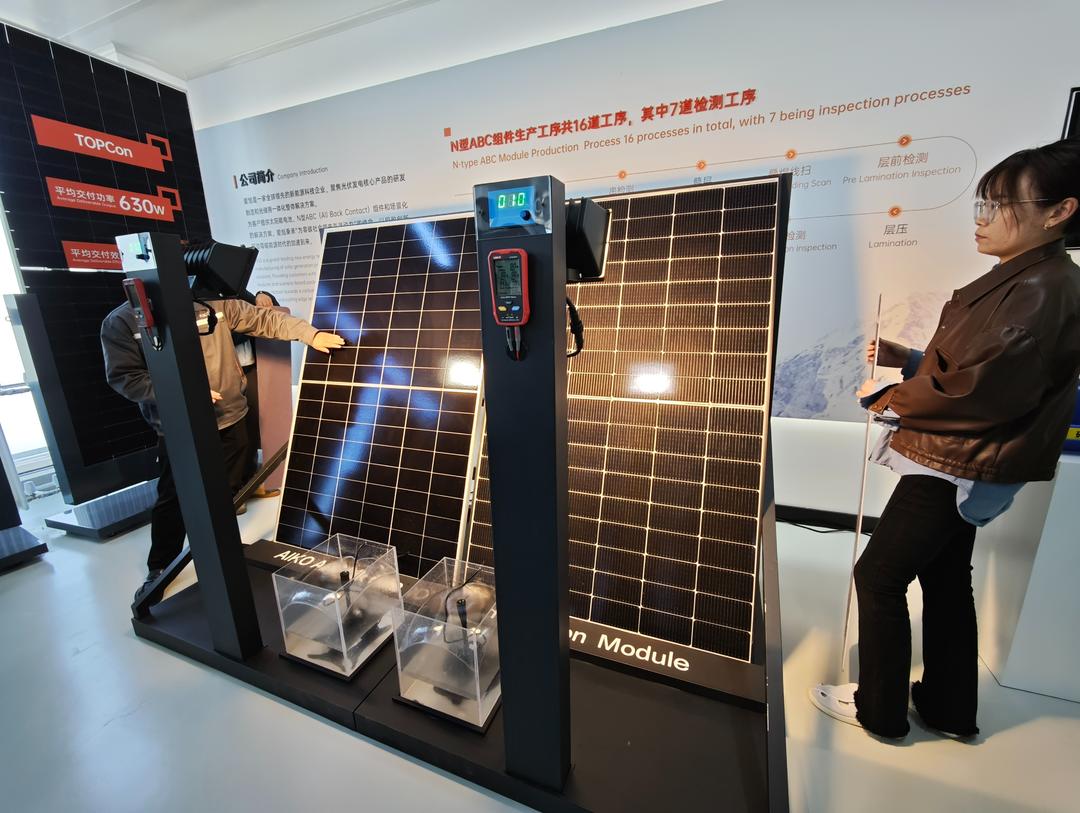
據(jù)愛旭濟南工廠相關負責人介紹,工廠以智能制造賦能綠色生產。一期10GW項目實現(xiàn)工業(yè)4.0與光伏制造深度融合。工廠采用智能化生產線,實現(xiàn)從硅片到組件的全流程數(shù)字化管控,生產效率提升30%以上。“整個組件生產一般需要4個小時。整個產線流動起來,12秒即可下線一塊組件!
穿行在生產車間,“讓每一片土地的陽光都發(fā)揮能量”“讓每一平方米的組件功率更高”“讓組件每一瓦功率發(fā)電量更高”……醒目的標語讓人印象深刻。
“濟南基地主要聚焦愛旭最新一代N型ABC光伏電池及光伏組件的制造,打造最具競爭力的綠色智慧工廠。目前組件首線已全面投入量產,量產效率達到24.6%,處于全球領先水平!眲⒕跋舱f。
在光伏組件量產效率領跑全球之際,愛旭濟南工廠也已成為零碳工廠的一個樣板。劉景喜表示,通過全自動化生產、智能化運作、智慧園區(qū)管理,打造集綠色、數(shù)字化、智能化為一體的智慧工廠。
實現(xiàn)零碳背后,離不開能源的綜合利用。據(jù)介紹,該工廠利用廢水再生、回用技術,減少水資源浪費。對內采用中水回用技術,回收利用率達30%;對外聯(lián)合起步區(qū),與孫耿片區(qū)的再生水廠共建全流程循環(huán)模式。再生水廠將工業(yè)廢水處理達到自來水標準,產水全部回用于愛旭工廠,實現(xiàn)項目90%水回收。
與此同時,愛旭濟南工廠利用余熱回收技術,減少能耗,降低碳排放。一方面,積極引入熱泵技術,實現(xiàn)廠務水系統(tǒng)、工藝廢水系統(tǒng)、熱回收率達95%以上;另一方面,引入乙二醇循環(huán)、主動式熱回收系統(tǒng),實現(xiàn)生產廢氣熱量回率達30%以上。通過這些舉措,有效降低冬季采暖負荷,減少了供暖的碳排放。
在工廠電力使用上,愛旭濟南工廠與政府及相關供電企業(yè)共同構建綠電方案,源頭上減少碳排放。
“通過技術及生產工藝創(chuàng)新,工廠達成了顯著的減碳節(jié)能成效——100%綠電使用、30%余熱回收、90%廢水利用,有效降低了傳統(tǒng)火電帶來的碳排放和資源浪費,提升了資源再利用與環(huán)保水平,契合了全球能源轉型和綠色發(fā)展的趨勢。項目全面達產后,預計年度節(jié)約用煤量2160萬噸,減少碳排放5384萬噸!眲⒕跋舱f。
以一個項目聯(lián)動一片、帶動一方。未來,愛旭濟南工廠將聯(lián)合起步區(qū)構建零碳產業(yè)園,助力片區(qū)實現(xiàn)千億產值目標,帶動濟南乃至山東的光伏產業(yè)集群化發(fā)展。
(大眾新聞·經濟導報記者 劉勇 見習記者 賈義航)

|